Getting Started
I was finally in a position to start construction on the observatory by mid-2023. I was mostly working alone, but for larger jobs that I just couldn’t complete myself, help was enlisted, such as a hiring a backhoe for trenching. I decided to build a round building for the 12-1/2-ft dome, and I already have a 14’x30′ metal building on site to use as the “warm” room. Once power and Internet are run it will allow connecting the two buildings together via the network.

Trenching to install a conduit for power and Internet, and dig a hole for the pier, were done in conjunction with running a water line from our well to a new garage and garden area. The ground here is a thin layer of soil over increasingly thick layers of underlying shale rock. The layers started +out so thin a shovel could break them up, but quickly became thick to the point that the small backhoe doing the job could not dig much deeper.

After cleaning out the loose soil and rock from the hole for the pier, it is about two and a half feet deep. The bottom is a thick bed of shale. A reinforced concrete pad will be poured on top of it before building the block pier base.
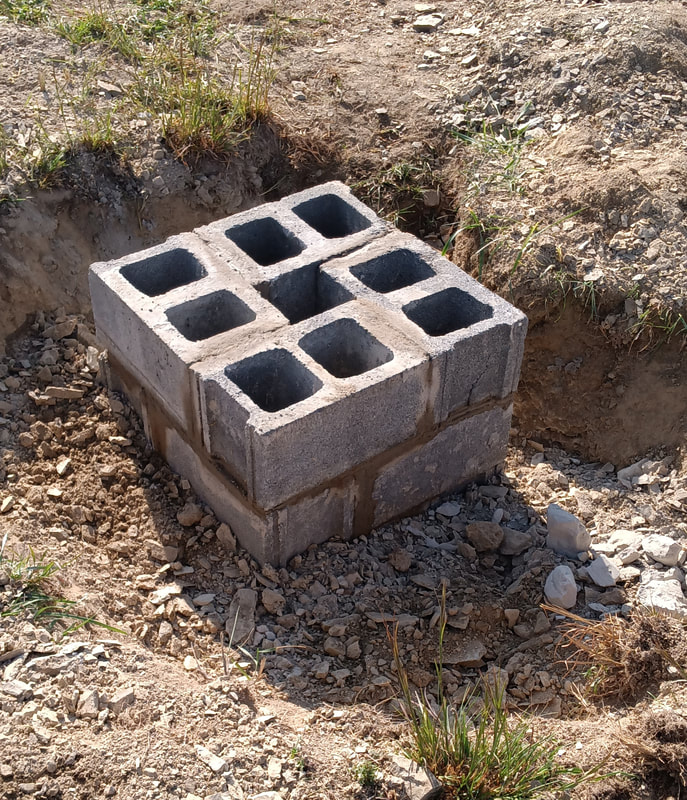
The block base is three rows high in the photo, and sitting on the concrete pad. Shale and dirt is being packed in around it as the hole gets filled again. Two more rows will be added as the observatory foundation progresses. In the end it will be about 4 feet tall, though a good portion of it will be underground. And it will be filled to the top with concrete once finished.
Building the Foundation

Starting to dig to pour a footer for the foundation. It will be about two feet deep to ensure the footer will be below the frost line. Another row of block has been added to raise the pier base high enough not to get dirt in it. All this digging was done by hand because I couldn’t afford to bring a backhoe back for just this one job.

After multiple days digging and shoveling, cut up pieces of cattle panels were put down as rebar, and the footer was poured. It took 26 80-lb bags of ready mix concrete, weighing over 2080-lbs. No wonder my back aches.
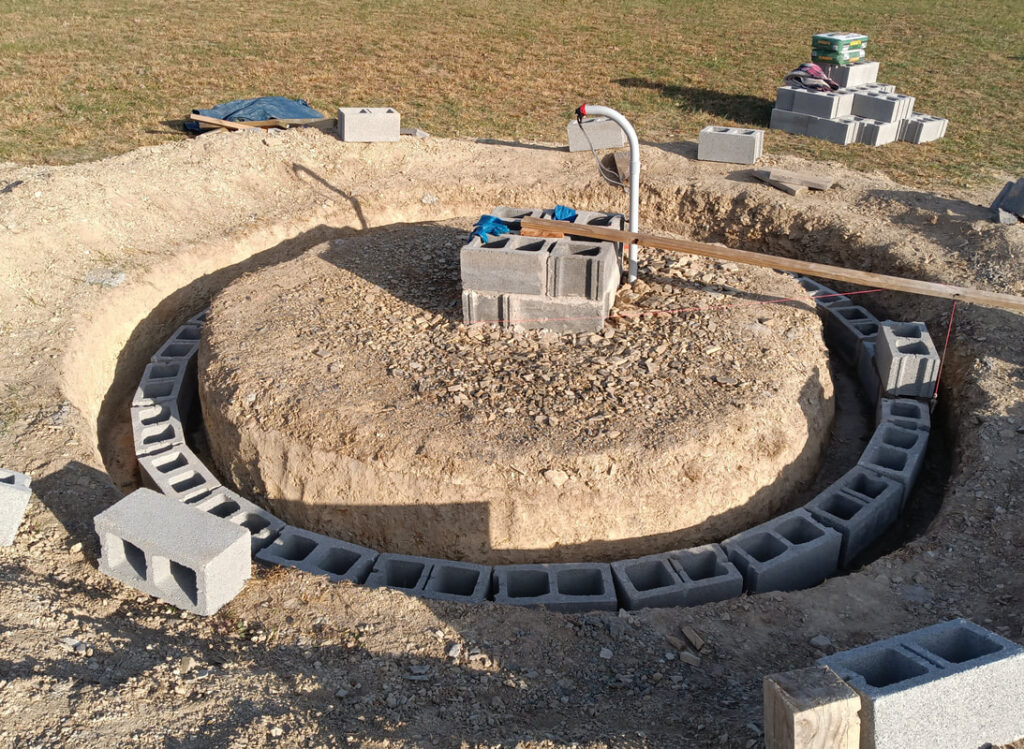
The first row of blocks is finished and just starting on the second row. Two rows will bring the foundation up to almost ground level. The outer diameter is 12′ 2″ and uses exactly 26 blocks for a full circle. I’ve never actually laid blocks before, but I’ve watched others do it since I was a kid, so I do know what needs done, more or less.

There are four rows total, and for the top two rows that are visible I switched to split-face blocks that match the house foundation. Actually they are leftovers from the house foundation, except I came up five short, and had to make a trip to the block company for more. Because of the doorway, there’s only twenty-four blocks per row for the top two rows.
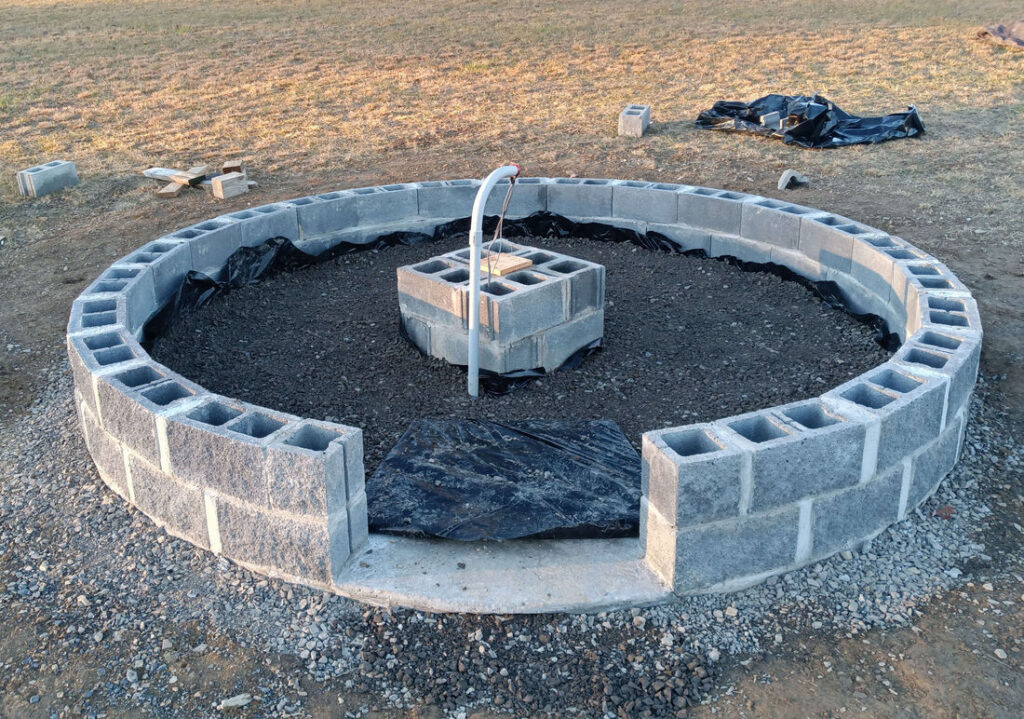
I worked all day on a Saturday to finish mortaring all the joints. It’s late Fall 2023 and the weather was alternating between cold, rainy days and the occasional nice day, so I worked every good day that came along. I’ve also cleaned up all the excess dirt from digging the foundation, both outside and inside. Then I laid down a vapor barrier inside and poured crusher run on top, thinking this would be good enough, and save the cost of pouring a concrete floor (not pouring concrete inside will come back to haunt me).
Constructing the Building
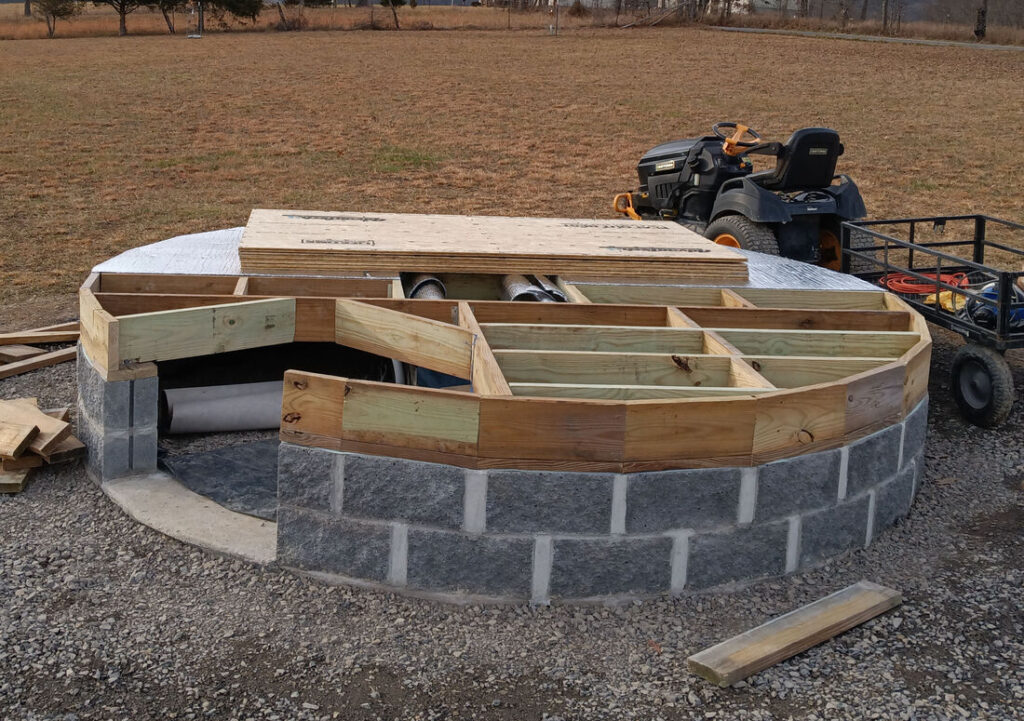
It’s late, late Fall of 2023 and I was hoping to get the floor done before it got too cold to work. The sill plate and outer band are made from individual block-length pieces joined together with metal plates and J-bolted to the foundation. The joists are 2′ X 8″ lumber and the sub-floor is AdvanTech sheeting. This as far as I progressed before the snow came, so everything ended up tarped over until Spring.
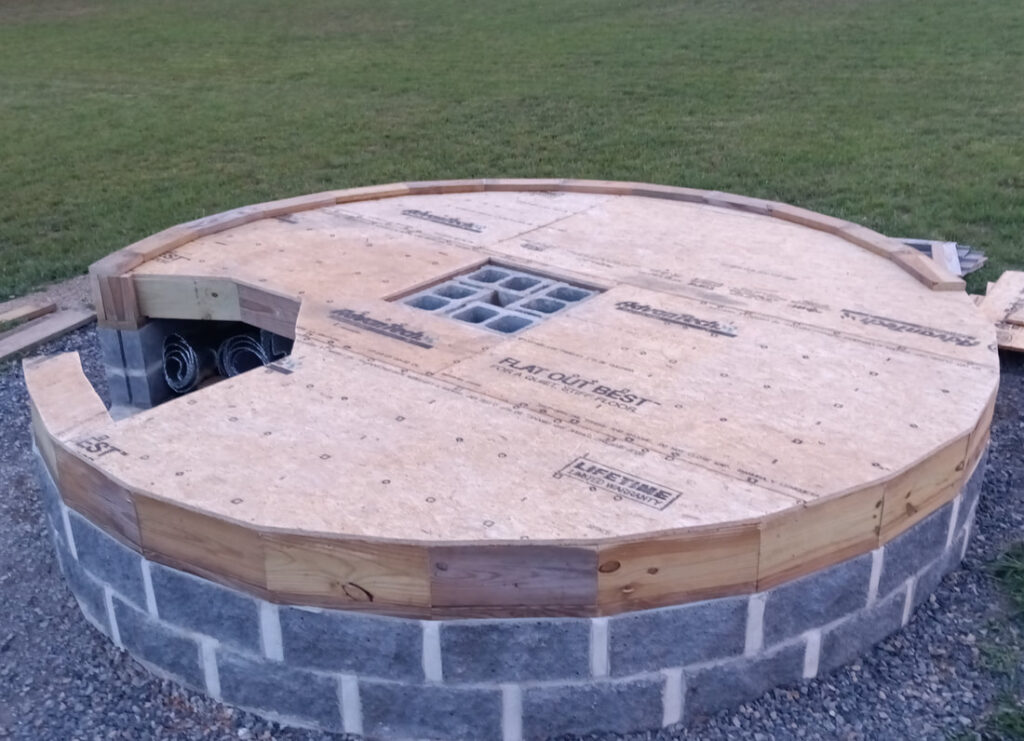
It’s Spring 2024 and the floor is finally done. The wall plate was in the process of being put down, and one final row of block has been added to the pier base, bringing it up to its final height. Also, the open cutout in the floor is for steps.
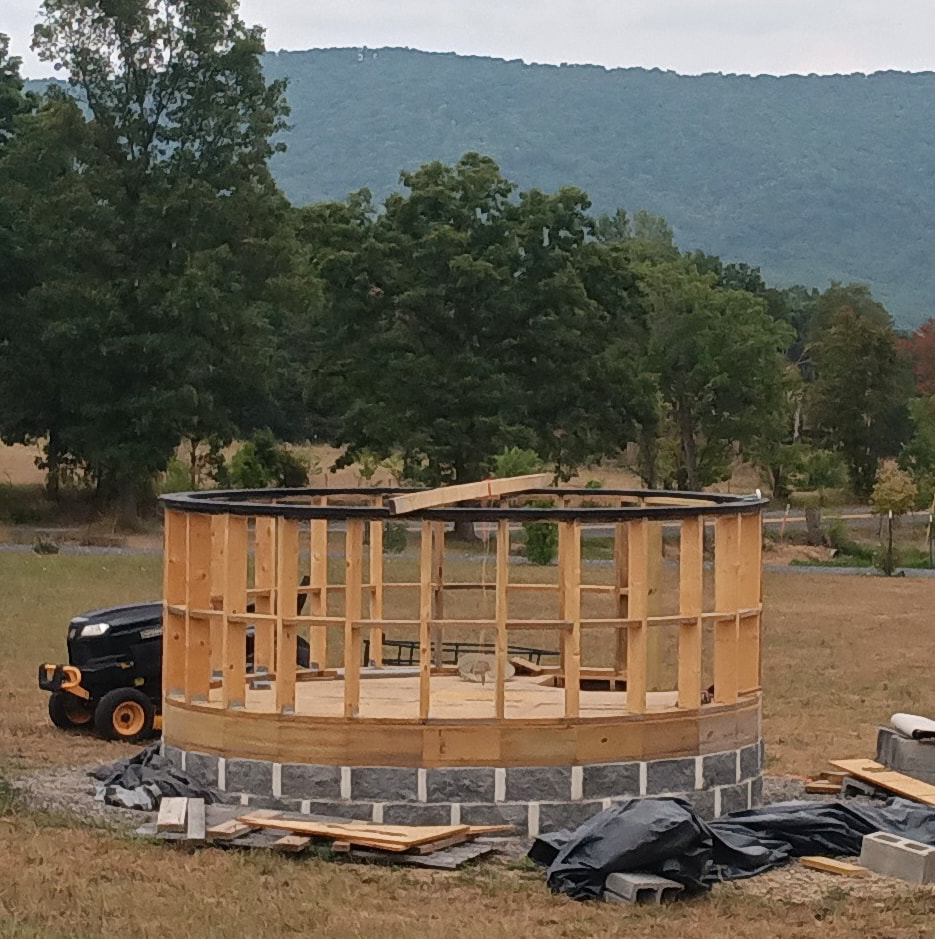
The walls have been studded up. The Ash dome comes with a dome base ring for mounting the azimuth wheels, but I don’t have a ring with this dome, so I had to make one. It’s cut from 3/4″ plywood in 4-foot sections. It is actually two rings stacked and glued together to make a single ring 12′-2″ in diameter and 1-1/2″ thick. In the photo the ring is painted black to seal it up in case of rain.
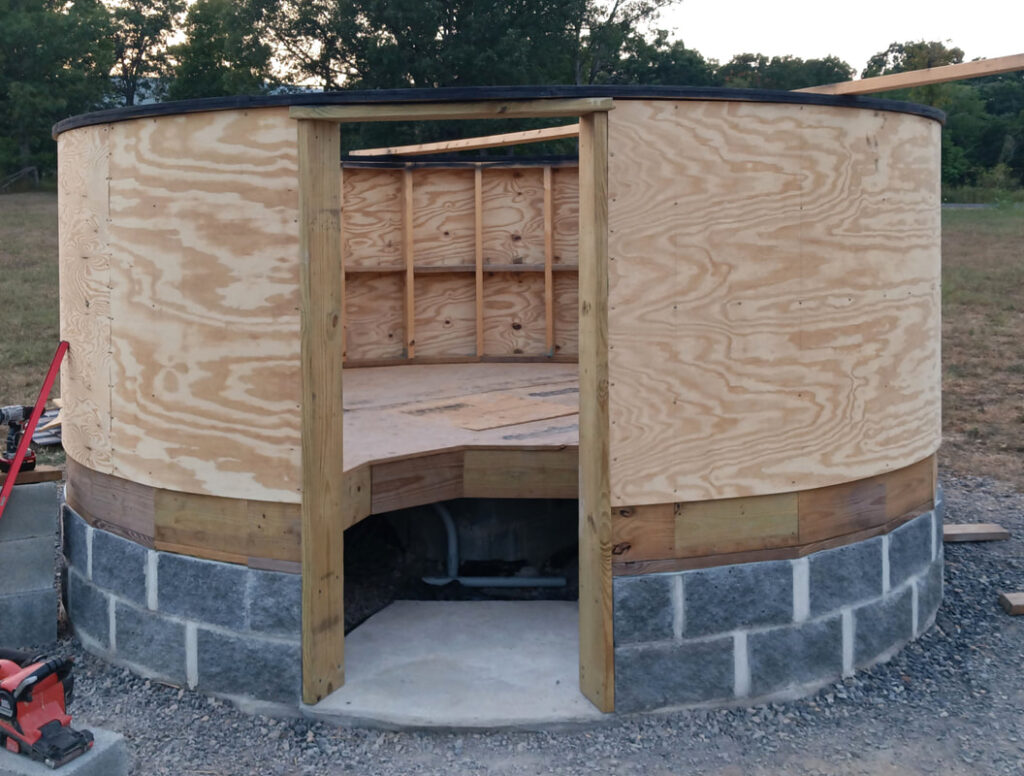
The wall studs had to be tweaked to ensure the building is as round as possible, and then 1/4″ exterior grade plywood was installed. Also in the picture, a concrete pad was poured in the entry way and the door was framed with pressure treated lumber. The ring on top was installed according to the Ash manual, being leveled with shims and bolted to the top of the wall with 1/2″ carriage bolts.
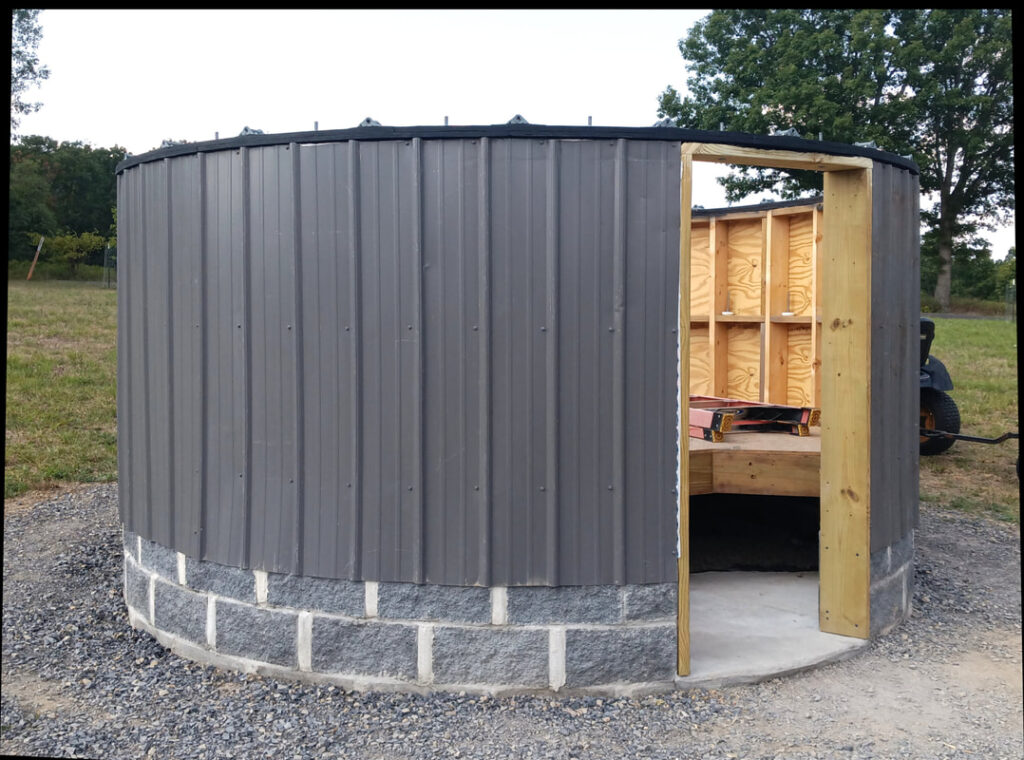
The metal siding was leftover pieces from the roof of the log home we built in 2018, and sold before moving here. It got kicked around for about five years, so it has its share of scratches, but it saved me money.
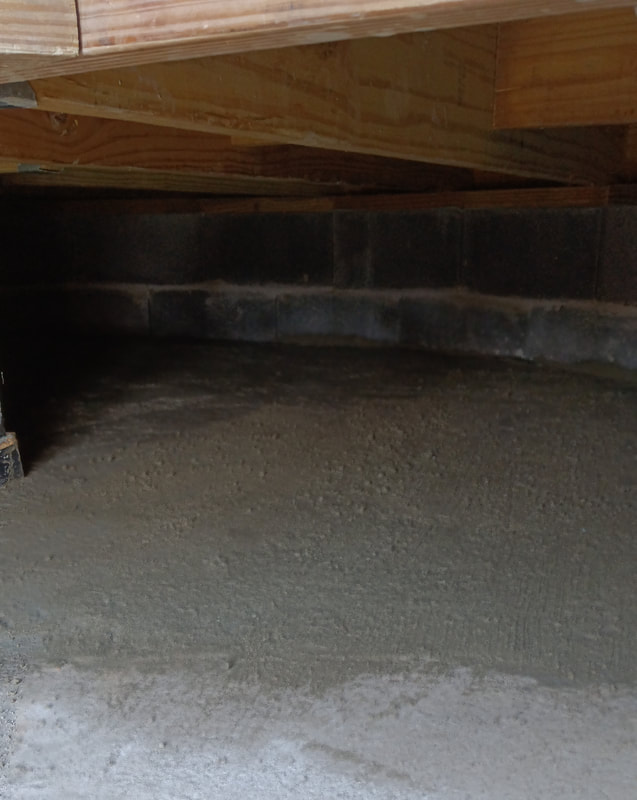
It’s now time for the plastic vapor barrier covered with gravel to come back and haunt me. It was a very hot summer, with temps hitting a hundred on a regular basis. My Australian Shepard liked to lay under the floor on those hot days, while I sweated away up above. Unbeknownst to me, he dug up the gravel, and the plastic barrier, in multiple spots while making himself comfortable. So I had to rake out the gravel, trim up and repair the vapor barrier, and lay in more cut up cattle panel for rebar so I could pour a concrete floor. Not an easy task now that the wooden floor is installed. I had to cut open the floor as well, but it’s finally done. This is what I should have done from the start.
Constructing the Dome

The dome rotates on twenty-three garage door rollers. These are 3″ polypropylene commercial rollers with sealed bearings and stainless steel shafts. The wheel mounts are galvanized, but had sat in a box for at least twenty years, so were heavily oxidized. Before installing them they were cleaned and coated with cold galvanizing compound. Under each mount is a 1/4″ thick neoprene rubber pad. After test fitting, the mounting holes were drilled through the base ring for 1/4″ bolts.

A lot of hardware was missing, and what was there was mostly corroded, so new stainless steel hardware was ordered. I’ve ordered over 600 screws and bolts, plus nuts and various types of washers.
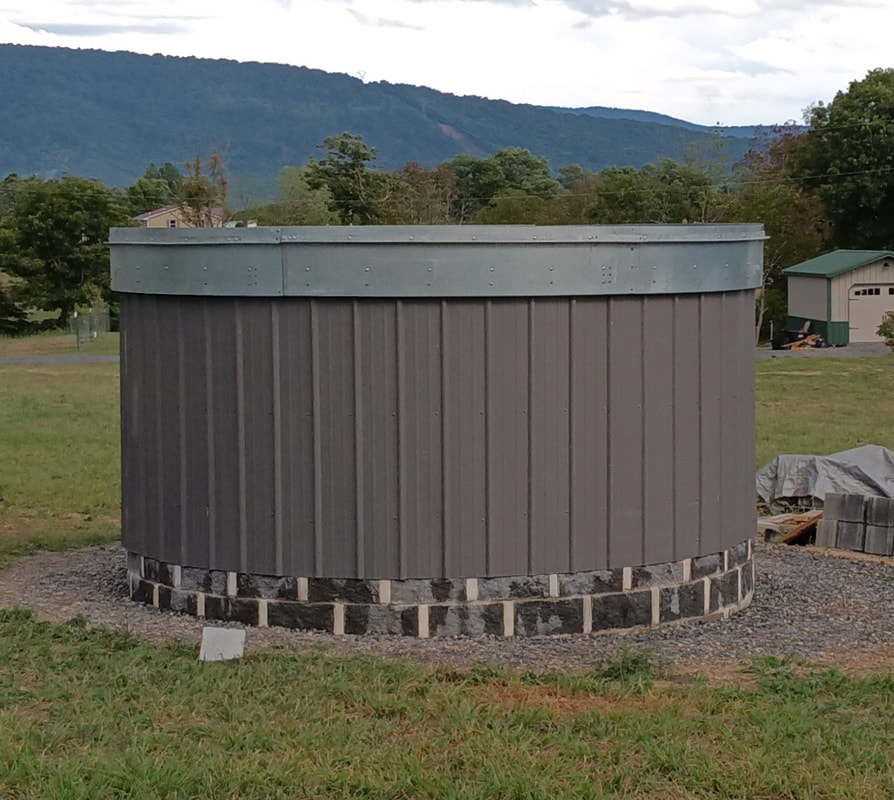
The dome base consists of six segments. The base ring had been previously assembled and drilled for bolts, but none of them were marked, so I had to sort them out by matching up mating bolt holes. Five of the six will slide right onto the rollers, but for the last piece I had to remove and mount the wheel track first, then slip on the segment from above and bolt it back together. The braces, gear track, and wheel track for each segment were already installed when I bought the dome, but I replaced all the old hardware with stainless steel.

This is a day I had long waited for; actually assembling the dome panels. On the first day of panel assembly, we (my wife helped) only managed to get 8 panels mounted because of all the prep work. A Lancaster dome has a ring in the top to tie all the panels together, and it has to be supported until a sufficient number of panels are added to make it self-supporting. The only hurry here is to get all the panels on before any windy days come along.

We hoped to finish installing panels on the second day, but didn’t quite get there. We’re getting faster as we go though, at this point we have 21 panels on.
We worked until dark and as we wrapped up for the day my wife spotted a train of Starlink satellites marching across the sky, heading eastward. They were very bright and still close together, so they must have been “released into the wild” fairly recently. I think this was on September 6th and I saw online that SpaceX had launched twenty-one Starlinks on August 31st, so I guess this was them.

The third day and all the panels are on. The two “missing” panels in the photo is where the shutter opening will be cut out. The ring in the top will also get cut out.
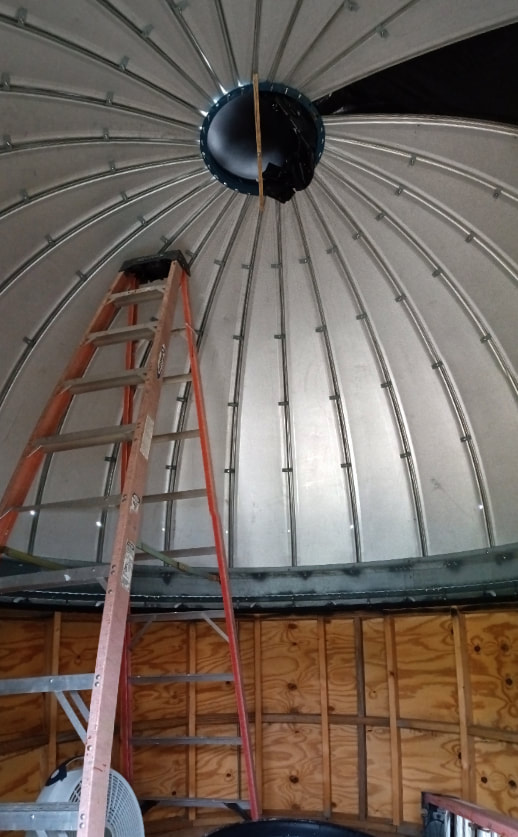
A look inside the dome reveals all the dome clips tying the panels together. These are zinc-plated and had also been oxidizing away in a box for twenty years, so they were coated with cold galvanizing compound as well. I was also short about seventeen clips, but I discovered Virginia Silo Company was less than two hours drive away and they not only had the clips, but gave them to me without charge.
Finishing the Interior and Pier

Finishing touches on the inside include a railing around the stair well, to prevent anyone from accidentally falling into it, not that I would know anything about that. Let’s change the subject. All the material for the railing was leftover from our front porch and rear deck projects on the house. The walls were insulated with reflective bubble foil before installing Luan paneling.
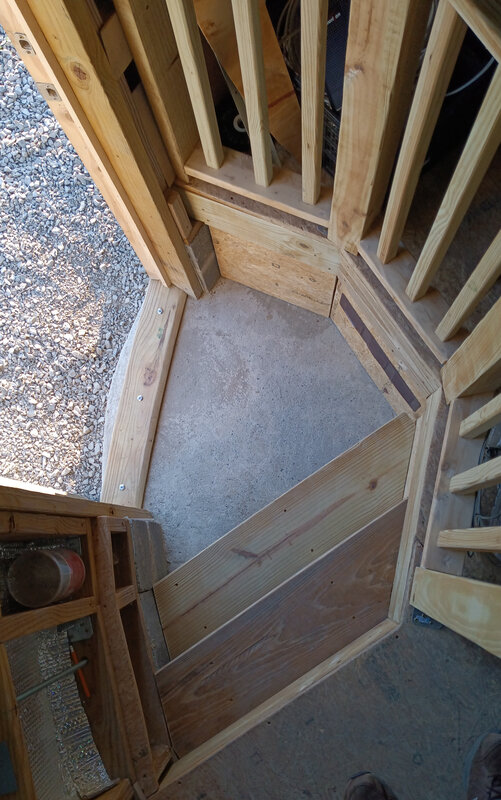
The entry and stairs have also been finished up. It’s two steps (three if you count the floor) up to the wood floor. The stairs are open underneath so no creepy crawlies have a place to hide. Panels were installed to close off the under-floor area, but a vent was added for air flow. The rails and steps will be finished with Australian Timber Oil. The door is not a standard size, it’s approximately 69″ high and 31″ wide, so one was custom made instead of trying to chop up a prefab door.

To finish the pier, the base was filled with concrete and rebar was added. I also installed a short conduit from the side of the pier under the floor up to where the metal pier bolts on top.
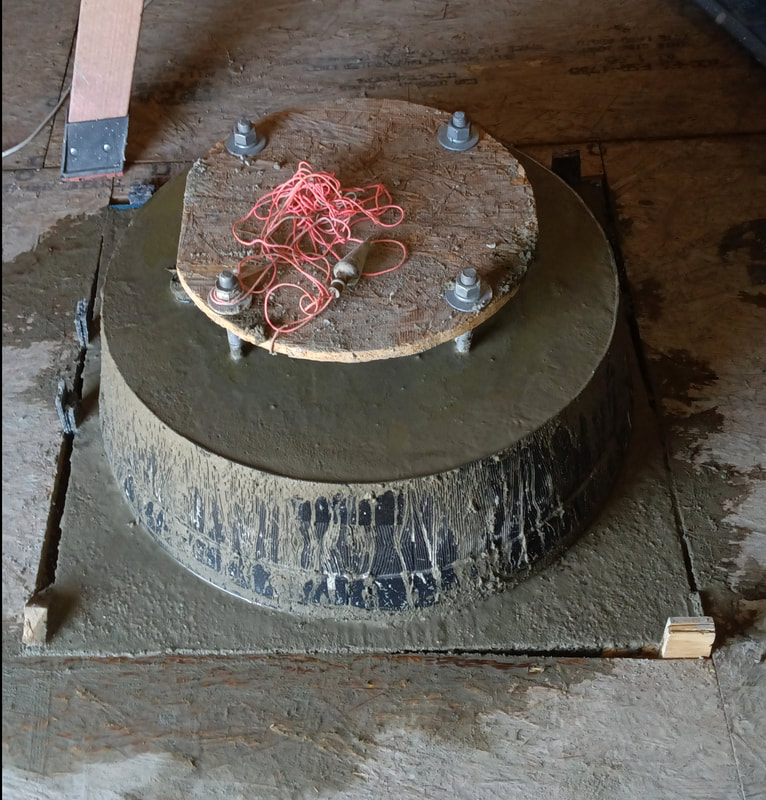
The concrete on the square pier comes up level with the subfloor and then transitions to a round base. It will be less of a trip hazard than having square corners jutting out. The round form was a large plastic planter from Tractor Supply, cut down to 7-1/2″ high, which will make the final pier height 60-1/2″. Galvanized J-bolts were set into the top for attaching the metal pier.
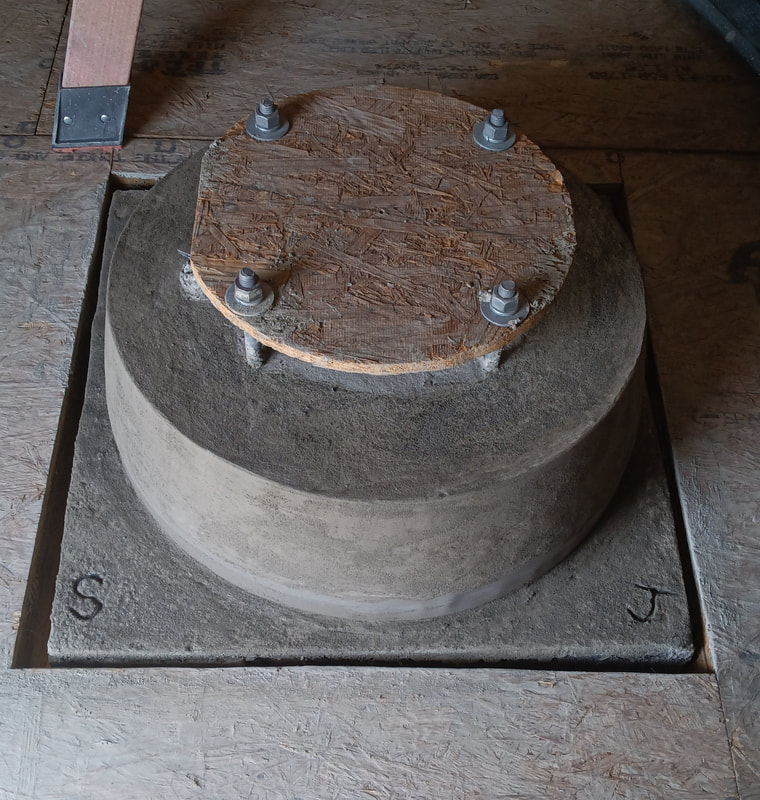
The finished base was allowed to set up for a couple of weeks before installing the heavy metal pier. Also, now that the forms have been removed, there is a gap between the floor and pier base, to prevent vibrations being transmitted to the pier. The base is also isolated from the concrete floor below, but the gap there is filled with foam to keep critters and moisture out.

I guesstimate the metal pier weighs at least 150 to 200 lbs. No way I’m picking that up by myself, so I lifted it into place with a chain winch hanging from a wooden beam supported by two ladders. The pier is adjustable from about 39 to 42 inches high, the center pipe is 10″ in diameter and is 3/8″ thick steel. The top plate and bottom plates are 1/4″ thick. the adjustable top plate and bolts are not yet installed.

Ready for paint. The pier has been set, the walls are installed, the entry way is done, and the floor was sanded. I even built a curved table out of leftovers, that fits tight against the wall. The open panel beside the table is where the cables from the pier come up from under the floor. That panel will get installed later.

And now there’s paint. I called it star chart blue, but Benjamin Moore calls it New York something or the other, I forget. I also have a speckled black rubber floor that I’ll put down once the dome’s shutters are finished and all the ladders are gone.
As I was assembling the dome I discovered I am missing some parts for the shutters and shutter tracks. When I purchased the dome I was told it was complete, but since there wasn’t a manual or a parts list, I had to take their word for it. Turns out there are parts missing for the shutter, the formed metal weather flashing for around the opening, the shutter spacers, and the curved garage door tracks for the shutter wheels to roll in. Also, all the rubber weather seals for the shutter are missing, as well as the motor mounts. A couple of metal fabrication shops are making the missing flashing, track spacers and the azimuth motor’s mount, but I can’t find any company that can bend the garage door track, so I’m going to have to work on that myself. Once I get the parts, and the weather warms up, I can continue working on the dome.
Last Edited 03/13/2025